Building Information Modeling has been a truly revolutionizing concept for the entire AEC industry. Bringing every aspect under the purview of a single digital model, BIM promotes efficiency and collaboration like never before.
BIM facilitates data exchange between several stakeholders involved in architectural design, engineering and construction domains.
Being a systematic blend of processes, policies, people information and technologies, BIM allows professionals to acquire deep insights on several aspects like design, cost, time, sustainability and facility management, among others.
In a way, BIM facilitates the entire construction cycle, paving way for higher growth in AEC domain. Here are 5 processes which have been positively impacted by the introduction of BIM:
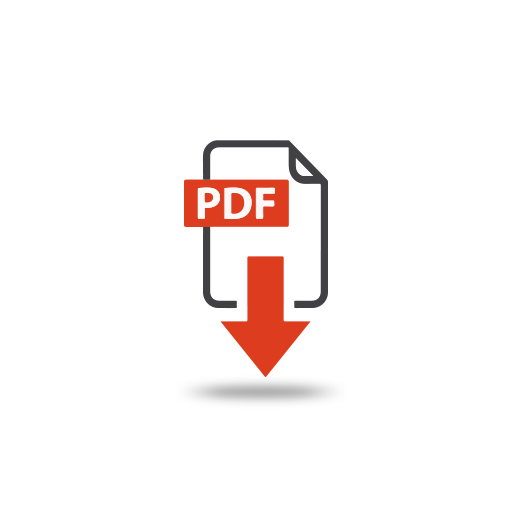
Don’t have the time to read the whole blog, no worries you can download it and read it at your convenient time.
1. Design Coordination- Clash Detection
Clashes are a pertinent cause of delays and failures of large-scale construction projects. When so many stakeholders like architects, engineers, planners, contractors and fabricators are working on a single project, there are high chances of clashes due to minimal coordination and collaboration.
Clashes can be either soft ones which are easily manageable with small amends or hard design element clashes, that require complete rework, leading to wastage of time, effort and resources.
Clashes can impact the timelines, making projects costlier and lengthier to complete, which has a cascading effect on scheduling, workforce management and logistics.
BIM can make it easier for all the stakeholders to collaborate on the design and other aspects for early coordination and clash detection. By resolving clashes within the 3D model and common data environment, many clashes can be reduced, minimizing design mistakes.
Modern BIM software like Revit can be used for verifying BIM models for overlapping or interfering elements. Similarly, other solutions like Navisworks also accelerates the process of clash detection early on. Planning based on BIM models reduces chances of clashes, reworks and reduces the cost of the project.
As informed decisions can be taken at the early stages, it saves valuable time and resources of engineers, contractors and designers, accelerating the process of project completion.
2. Quantity Take-offs- Generation of BOQs and BOMs
BIM is capable of accurate generation of Bill of Materials and Bill of Quantities with its quantity take-off function. 5D BIM Model focuses on the preparation of quantity estimation by connecting a 3D model, its different elements, parts and components to a cost estimator.
Such kind of automated cost estimation promises high-grade efficiency and saves time in re-estimation in case the geometry or quantity is changed.
The on-screen quantity takeoffs promote improve decision making and eliminate prediction and guesswork out of logistics, scheduling and costing. Planners can use 5D BIM models to communicate better with sub-contractors about costs owing to a detailed and accurate BOM that gets updated in real-time with design changes.
3. Fabrication Process- Generation of Shop drawings
BIM can be used for efficient design, management and control of shop drawings and fabrication process. The digital design flow for fabrication and shop drawing design promises greater accuracy, faster design development and minimal potential design issues.
With the help of BIM, designers can enjoy greater control over the final product by identifying and eliminating issues at the design stage itself.
As everyone understands that fabrication can be a time-consuming process involving high costs, using BIM for shop drawing designs and fabrication can reduce costs, save time and resources efficiently.
BIM can be used for digital fabrication and development of shop drawings with a comprehensive design-to-fabrication workflow that improves coordination and quality of the end result.
Subscribe to Our Newsletter
* We don’t share your personal info with anyone. Check out our Privacy Policy for more information.
4. Facility Management
One of the most fascinating aspects of BIM is its capability to embed all the information required throughout the project lifecycle in a single model. This also includes information about facility management which is essential after the handover of a building. The collaborative approach that makes it easier for all the parties to access and coordinate on several aspects streamlines information flow and eliminates chances of miscommunication.
Using BIM, all the systems and components associated with regular maintenance, sustainability and energy efficiency can be effectively managed. All the systems can be visualized and optimized even before the actual construction, which makes it easier to reduce costs and also simplifies the process of coordination after project completion.
BIM can also be used for achieving energy efficiency by evaluating various aspects during the design phase itself. When it comes to facility planning, all the documentation related to several components is present in a single digital model, which makes the work of facility managers easier after the contractor moves out of the picture.
5. Re-designing of an existing building- Generation of As-built model
BIM can also be used for redesigning of an existing building. By using a mix of original design plans, laser scanning of the actual building and other innovative practices, an integrated digital model can also be created for a redesign.
BIM can support as-built models of old buildings and existing facilities and can modernize the entire design and coordination process, bringing every stakeholder on a single platform. Using the BIM approach, retrofit and improvement opportunities within old buildings can be discovered, making buildings cleaner, energy-efficient and easier to manage in the future.
Final Words
The scope and implications of BIM technology are quite broad. This single concept can revolutionize the entire value chain within the AEC domain, paving way for greater efficiency and productivity for everyone- designers, contractors, building owners and other stakeholders. Discover how you can utilize BIM for your next project today with our experts. Get in touch now.